自動化編程的重要意義
隨著加工行業競爭的日趨激烈,企業不斷尋求在保證加工質量的同時降低加工成本的方法。很多企業首先想到的是引進先進的自動化設備,比如帶有自動換刀的大行程的數控機床。隨著機床加工性能的提升,如何在不增加人員投入的前提下“餵飽“機床,通過提高機床稼動時間來降低生產費用,是很多企業面臨的難題。提高編程效率,保證數控程序的質量不隨編程員個人技術水平大副變動,利用自動化的數控程序帶動自動化的無人加工過程,是這類企業需要解決的核心問題。
孔槽類特徵的自動化編程
對於孔槽類典型規則特徵的編程,大部分編程軟件都有了相應自動化的解決方案。儘管如此,還有不少企業在使用繁瑣的手動編程。CAD數據上孔深,倒角等已經存在的幾何信息不能被充分利用,而是需要額外構造點、線為編程作準備。加工中,還存在大量的由機床操作工人操作控制器實現孔加工。這樣的加工方法,費時費力的同時無法保證加工質量。
那麼,高自動化的孔槽類典型規則特徵的編程應該是怎樣的呢?首先,所有CAD中現有的能夠提取出來用於加工的信息應該被充分利用。這裡就設計到特徵技術,既將設計數據中的孔槽自動轉化為加工數據中的孔槽。這個過程的要求是不能存在特徵的遺漏,以及特徵的錯誤識別,這也是自動識別相對人工選取的最大優勢。其次,所有孔槽應該可以根據類型,加工方向自動分類。根據類型分類是因為藉此可以優化刀具的選取以及加工順序,加工方向分類可以方便在定軸加工中根據裝夾位置框選被加工元素。最後,只需要將特徵與加工模版相連接,根據提前定義好的加工順序自動選刀,自動編程。
所有特徵可以自動按照類型和加工方向分類
Tebis使用Job Manager管理程序,根據裝夾生成刀路,而不是簡單的為每一個孔槽生成單條刀路,這樣一方面就可以利用軟件對加工順序和抬刀進行優化,另一方面可以大大降低的機床操作人員需要不斷調入程序的繁瑣工作。從編程室出去的程序就可以直接在機床上運行。
Tebis一鍵生成不同類型孔的鑽孔加工
使用特徵自動識別技術並結合編程模版能夠實現規則特徵的“一鍵“編程,支撐這套流程的背後是企業標準化的製定和相應的在實施前期的投入。特徵庫以及編程模版無法在企業間直接拷貝,應結合企業自身情況和經驗進行製定。而且,整個刀具庫、特徵庫、編程模板的維護是一個動態的過程,想達到完全“一勞永逸“是不可能的。企業只有自身消化整套自動化編程流程,才能在激烈的行業競爭中快速的應對變化和挑戰。
非規則特徵的自動化編程
Tebis不僅支持規則特徵的自動編程,比如孔、方形槽的加工,還支持不規則特徵的自動編程。這裡一個典型的應用就是大型沖壓模具刀塊安裝平面和限位面的加工。當前常見的處理方法是手動對其分別進行編程,這裡實現自動化編程的難點是限位面和安裝面幾何上的相對位置是不固定的,其不像方槽的側壁圍繞底面一圈,而是通常情況下一側是開放的,有時限位面甚至會延伸出安裝平面。
沖壓模具刀塊安裝平面和限位面
使用Tebis可以將刀塊安裝面和限位面作為一個特徵自動處理。如果刀塊安裝平面和限位面之間存在倒角,這部分區域也可以被自動考慮進去,限位面和安裝面一起被識別出來,而不由於倒角的存在被識別成單個的平面和側壁特徵。用戶可以在特徵識別過程中,根據需要,在不退出當前界面的情況下快速對特徵進行編輯,比如添加額外限位面,構建輔助連接面等。
Tebis將刀塊安裝面和限位面作為一個特徵識別
在實際加工中存在很多上述這樣需要考慮側壁面的底面加工,Tebis在2.5D平面編程功能中允許指定側壁,這樣,通過Tebis識別出的限位面會自動的在編程中被選取。利用定義好的編程模版就可以一鍵編程了。
在平面編程過程中,側壁面也會被考慮
將刀塊安裝平面和限位面作為一個整體去考慮,而不是簡單拆分成平面和側壁的組合,在實際加工中具有重要意義。這也是Tebis2.5D自動化編程相比其他同類軟件能夠在實際加工中得到應用的原因。由於側壁和底面都存在毛坯餘量,因此從加工順序上來看,應該先將側壁粗加工到底面毛坯餘量的高度,然後再粗加工底面。Tebis在這裡可以將底面毛坯餘量值作為一個變量設置在側壁的加工程序中,而且變量值可以根據毛坯的實際情況設為常數或者讓編程員根據掃描結果手動輸入,給客戶依據企業內部具體工藝流程靈活設置編程模版的可能性。
自動生成的刀塊安裝面和限位面粗加工刀路
借助全機床仿真提高製造安全性
採用無人加工可以幫助企業大大降低人工成本,但目前大部分無人值守的單件加工僅局限在半精和精加工環節。原因有以下幾點: 首先,大形面的精加工抬刀少,工件雖然是三維曲面,但相對平緩。其次,精加工本身步距值小,一個大形面的精加工程序運行下來往往超過十個小時。在加工中出現撞機危險的常常是在機床頭抬刀移刀的時候,機床在運行G00指令快速定位,容易發生機床頭撞擊夾具或工件。為了降低撞機的風險,通用的做法是降低進給,增加抬刀到安全平面的次數,這樣保守的做法是以犧牲機床加工效率和依賴機床操作人員快速反應為基礎的。因此,如何生成安全的程序,在編程過程中就考慮到各種碰撞的可能並採取相應措施,是解決這類問題的關鍵。
Tebis全機床的加工仿真環境
Tebis支持全機床的加工仿真,在軟件中一比一的建立真實加工環境,所有出現在加工區域的元素,比如夾具、激光測刀儀等都被建立在虛擬環境中。值得指出的是,Tebis的全機床仿真是編程過程中的仿真,而不是簡單的編程過後的檢查。編程員從裝夾規劃、定軸加工角度到機床各軸的初始設置(比如帶W軸的龍門銑床),均可利用虛擬機床模型來進行,機床宏可以提前設置到機床模型中,真正作到完全仿真真實的加工環境。對於大型工件,可在規劃裝夾時考慮機床加工極限位置,充分利用工作空間。
檢測工件和刀具的碰撞
對於2.5D的碰撞元素的指定,通常有兩種方法。如果企業採取對整個鑄造毛坯進行掃描,可以利用掃描數據進行碰撞檢查。這種方法的好處是毛坯模型完全反映真實情況,對於不同毛坯厚度的區域無須單獨指定。但如果工件尺寸較大,相應的計算時間會比較長。此外,用戶還可以不通過掃描毛坯來進行碰撞檢查,對於大部分加工區域,設置標準毛坯厚度,對於毛坯實際較厚的區域,還可以由用戶單獨指定。在不使用掃描毛坯的情況下,需要用戶指定可能發生碰撞的曲面,比如工件上高聳起的區域或陡峭側壁,相比使用毛坯模型,這種方法的優點是靈活且計算速度快,缺點是半自動化且存在一定風險。企業應結合現有流程和工件特點選取合適的方法。
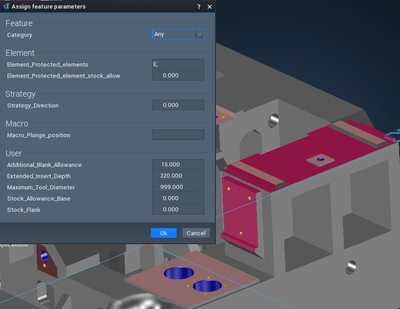
為導柱平台指定碰撞檢測元素(紅色)
總結
採用自動化編程技術已經是當今製造企業實現穩定快速發展的唯一方法。實施自動化的程度需要由企業根據自身的情況來決定,同時也受到CAM技術發展的製約,想要依靠計算機針對不同零件完全自動生成合理高效的刀路依靠現有技術是無法實現的,儘管如此,製造企業通過運用現有的自動編程技術大副提高製造效率、降低人工成本的潛力是巨大的。建立自動化編程流程的核心是製造過程的標準化,需要將所有相關因素都考慮進來,比如刀庫、設備、模版管理等等。2.5D的加工存在抬刀移刀多、加工元素不規則、碰撞元素多等特點,為自動化編程增加了難度。Tebis將刀具庫、特徵模版、加工模版和虛擬機床技術緊密結合,在實現最高自動化編程的同時確保程序的安全性,幫助企業充分利用生產資源,節約人力成本。