隨著模具中心加工任務的增加,以往隨性的工作方法與工作流程,已經無法滿足正常的工作需要,如何面對緊湊的工作節奏,順利的完成好各項工作,是需要我們及時去探索、深入研究的課題。通過近兩年以來的項目信息採集和整理,並多次約會機加和鉗工商討,制定出了多項技術標準,並最終彙編成數字化編程模板,這一規範的形成,為編程工作的統一性創造了條件,從而有效提升了整體工作效率,是一次新的嘗試,也是一次新的突破。
數字化編程模板的創新思路
什麼是數字化編程模板?
數字化編程模板的核心關鍵詞是“規範”,通過定義與編程有關的各項技術規範,實現編程全過程的標準化與自動化管理,簡化編程流程,減少人為參與與陪產時間,提升編程工作效率,實現產能更大化的重要形式。主要模塊包括了色系標準、數據標準、分面原則和標準工藝等。
數字化編程模板的作用?
標準化的數據色標,實現數據批量選取;標準化的數據結構,實現數據的統一管理;通用性的分面原則,縮短新員工適應週期,減少輔助工時;通用性的標準工藝,統一部門工作流程,減少返工與調整。
數字化編程模板的操作內容
標準的數據屬性管理
數據的管理方式根據其屬性一般有:類型、形狀、顏色等。而顏色作為最直觀的數據屬性,其可識別性為數據的可操作性提供了更大空間。
顏色,在數據管理中亦稱為色標,不對數據的功能與作用產生直接影響,往往不被重視,以個人喜好所確定,但在多次對複雜數據的處理過程中發現,不統一的工作方式無論是對前期數據的處理,還是後期的數據交接,都會帶來麻煩,如何運用好這一數據特性,為我們的工作帶來便利,需要我們引起重視。
首先,為了增強數據的辨識度,我們通過面片的功能對色標進行定義(而不是以零件來確定),從功能性上使得不同零件的色系標準達成一致,同時考慮到零件的複雜程度不同,設置一個主色標,外加多個備用色標,使得色系標準的通用性盡可能的提高,具體實施規範如下:
通過標準的色標,我們能夠快速的實現數據的統一選取,並對數據功能性及加工要求一目了然(結構、型面;粗加工、精加工;讓位、緊壓等),提高整體工作效率。
標準的數據格式管理
數據格式是對數據內容、數據要求的基本體現,是各項工作操作的基礎。
與數據色標類似,首先必須排除數據本身存在的差異對規范建立的影響,以數據功能性作為數據管理的標準,確定統一的數據格式。
本部門工作所涉及的數據類型包括了加工數據與編程數據兩部分:
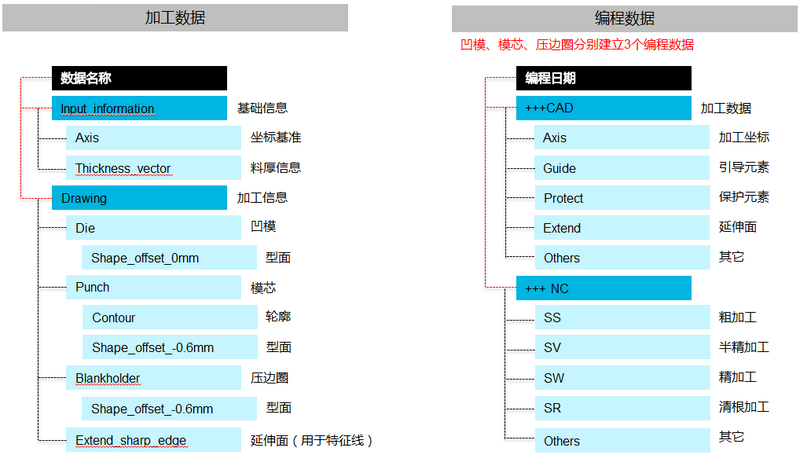
加工數據,包含了所需加工的全部內容,可理解為編程數據的上游環節,其標準格式已在多年的部門間交流過程中達成共識,整體結構清晰。
編程數據,定義了加工輔助元素層(+++CAD)和NC程序層(+++ NC),其內容較多且雜,實現統一管理後,將更好的提升數據流通的便捷性。
現初步定義加工輔助元素層包括加工坐標、引導元素、保護元素、延伸面和其它元素等所需信息,今後還將根據實際使用情況,做相關內容調整,而NC程序層的定義,對應了常規的加工工藝過程,整體格式確定,便於理解。
標準的數據分面管理
分面,作為新制模具編程的重要環節,需要對數據的內容、編程規範、加工工藝都有一定的了解,經驗的積累需要時間,無法實現前期高效的開展,這就對新員工更快的融入工作節奏,帶來了困難。
為了簡化這一重要環節,使得編程任務能夠更好的開展,加快新老員工之間的技術傳承,根據經驗把原本這樣一個靈活的工作,轉換為標準化的工作,將相同零件的分面原則進行確定,並製定相關的文檔,供參考,保證分面原則的基本框架唯一,之後再根據零件所特有的造型特徵進行局部的優化,就可以比較快速的完成好數據分面的工作。具體規範如下:
分面的總體思路是:首先根據產品的功能性,將數據進行劃分,之後再根據編程策略的選擇,和加工工藝等實際操作的需要,進行二次細分,保證後續的編程工作盡可能的順暢。
標準的編程工藝管理
工藝作為編程工作的嚮導,是保證加工質量的重要紐帶。
工藝的隨意或不確定,可能造成後期模具加工過程中的反複調整,直接影響模具整體的加工效率,而評判工藝的合理與否,需要與實際相結合,必須符合部門在軟件和硬件方面的能力條件,並不斷嘗試,逐步形成規範。
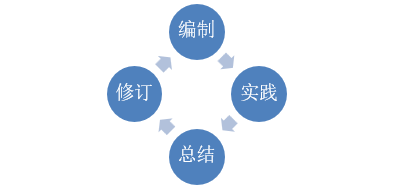
通過VW511側圍、SK372側圍、SK326翼子板、VW326車頂和VW416車頂多個項目的實踐,確定了模具中心的自製件OP20工藝標準:
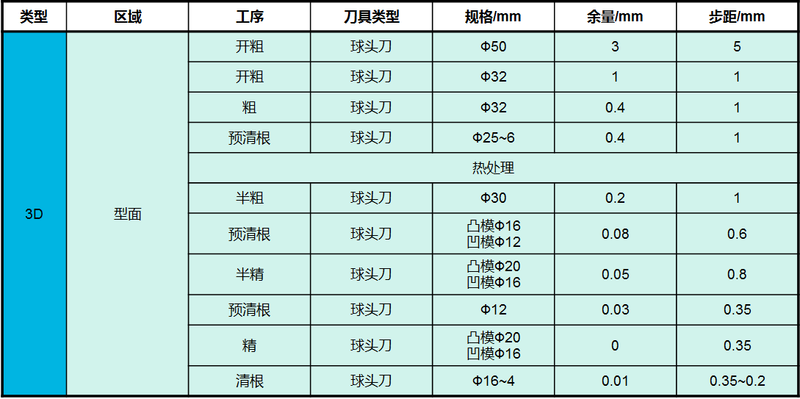
這樣一份規範的落實,銜接了工藝、編程和機加3個部門之間的工作,工藝編排,有依可尋,可操作性更強,編程操作,無需多慮,質量結果穩定把控,機床加工,提前準備,硬件設備保證齊全,使得多項工作可以提前開展,提前準備,減少交接過程中的分歧。
配合標準工藝,我們還將預先建立NCjob標準編程庫,將各項工藝參數填入,實際操作時可直接調用並作略微調整,就可以較快速的完成好程序的編制。
數字化編程模板的試用
模具新制編程過程可以分為:數據準備、型面劃分、Ncjob建立、參數設置、刀路計算、刀路優化和安全檢測這樣7個環節,對應工作內容:色系標準與數據標準將減少數據準備用時;分面原則將簡化型面劃分工作;而標準工藝可促進Ncjob建立和參數設置工作的有序開展。4個主要編程環節的工作效率,將在數字化編程模板的幫助下得到有效提升。
為了更好的分析數字化編程模板的運作效果,我們還通過翼子板零件進行了兩次試驗。
試驗分為兩個階段(對比項目為SK326翼子板OP20的首次新制):
第一階段為摸索階段,意在確認模板運作情況,使用已劃分好型面的SK326翼子板OP20數據(未進行數據準備及型面劃分工作),相同環節,模擬結果較之前,整體效率提升約40%。
階段一

第二階段為實踐階段,意在確定模板的可行性與通用性,使用全新的PA翼子板OP20數據,完全模擬全部新制編程過程,結果表明,整體效率提升也能有35%。
階段二
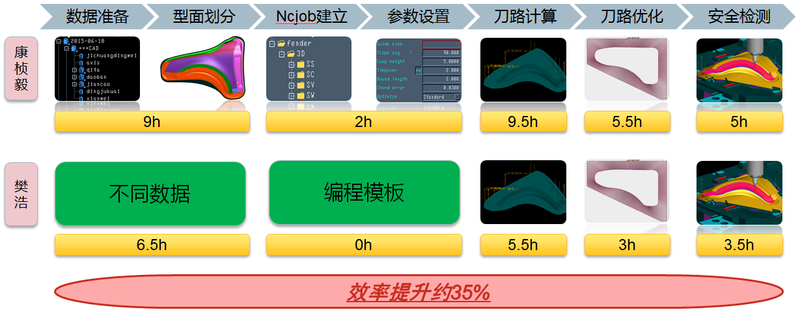
通過這兩次試用,肯定了數字化編程模板的作用和價值,為今後的投入使用做好了準備。
數字化編程模板的實踐
經過半年多的積累,借助VW326和VW416車頂OP20新制的機會,對數字化編程模板的可行性進行了實踐。
車頂造型簡單,無特殊結構,模板的各項規範能夠準確落實到位。
在VW326車頂OP20的加工過程中,現場反應,部分程序切削量大,導致加工速度慢,刀片的更換也較頻繁,建議調整,經確認,發現問題的關鍵在於對凹R角的處理不到位,加工餘量過大。
之後對VW326車頂OP20進行了工藝和編程的總結會簽,並在VW416車頂OP20項目中做出對應調整,使得VW416車頂項目的總體加工效率提升,程序的調整與更改次數減少近50%,從而基本確定了初步的標準工藝方案:
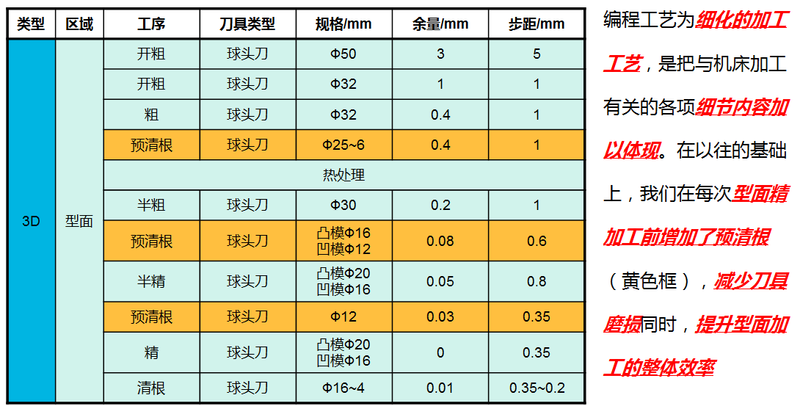
原基礎上,在型面加工前增加了預清根(黃色框),減少刀具磨損,同時,提升型面加工的整體效率
不僅是效率,兩個項目的加工質量也較穩定:
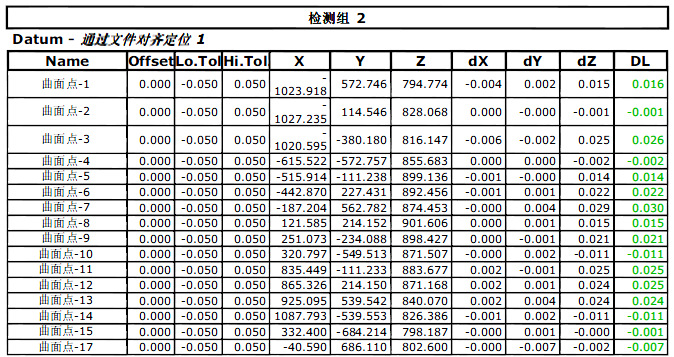
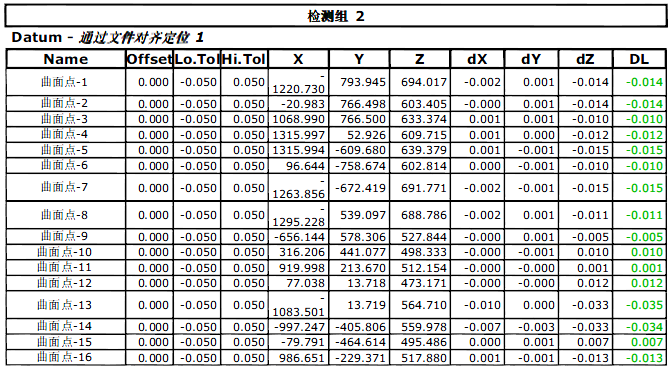
該項目編程員新制經驗為零,基礎學習時間也僅半年不到,但整體完成質量良好,得到了多方的認可,說明數字化編程模板的作用是明顯的,效果是有益的,但今後如何在其它複雜零件中全面落實,還需要一定的項目積累,和後續的刷新機制,來逐步完善數字化編程模板的內容。
小結
數字化編程模板是自動化編程工作的重要內容,自自動化編程工作開展以來,一直處於不斷收集過程中,在簡單零件中的應用已初見成效,後續側圍、翼子板等複雜零件中的實現還需要進一步的嘗試和實踐,其中的難點,毋庸置疑,由於零件的造型不同,工藝7要求不同,很難保證模板的覆蓋面能夠到位,這就需要我們去尋找規律,化整為零,將工作做到實處,實現全方位的高效的自動化編程管理。
作者:倪為華,上汽大眾汽車有限公司